.jpg?width=750&height=715&name=YSB55w%E5%8F%97%E6%B3%A8%E7%B5%82%E4%BA%86(E).jpg)
Overview
- High bonding accuracy and x3 productivity of conventional machines!
- This brings a New Era in Semiconductor packaging for the expanding flip chip market.
- High-Speed 8-die simultaneous pickup & simultaneous transfer achieve 13,000 UPH
- High-Accuracy ±5μm (3σ)
- High-Quality & Flexibility
Features
- High-speed bonding through parallel processing enabled by a dual flip head and an 8-component synchronized bonding process
- Outstanding positioning accuracy with a high-rigidity frame and control algorithms
- Bump recognition camera for high-performance positioning alignment
- Compact force control heads
- Compatibility with a wide range of flip-chip sizes from 2mm square to 30mm square
- Easy-to-configure Dipping station
Usage examples
Bonding process
High-Speed 8-die simultaneous pickup & simultaneous transfer achieve 13,000 UPH
1.Dual bonding heads Multi-nozzle (8 nozzles per head)
Two 8-nozzle heads with compact design enable high precision force control and also support thin die processing.

2.Dual flip heads
Achieves high-speed pick-up by parallel processing with 2 flip heads.

3.Multi-die supply
Equipped with 2 supply units for each flip head unit. Feeds flip chips with no time loss!
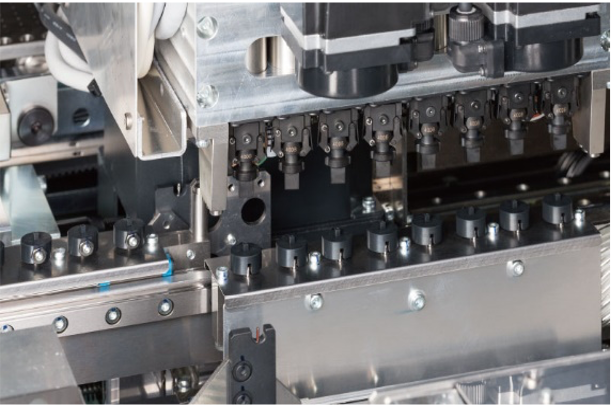
High-Accuracy ±5μm (3σ)
1.High rigidity frame & beam
Meticulous structural analysis and test verification achieve both high-level accel-decel drive and high-precision.

2.Linear motor/driver designed in-house
Unique dedicated design gives high-speed along with superb positioning accuracy.
*Example of measurement results with shaft-spindle stopped

3.High resolution chip recognition camera
Missing bump check and precise position alignment using bump positions.

4.Maintaining high placement accuracy
Our in-house developed MACS (Multiple Accuracy Compensation System) has been upgraded and now achieves bonding accuracy ±5μm (3σ). Original heat analysis & heat compensating algorithm realizes consistent placement accuracy.
High-Quality & Flexibility
1.Newly developed dipping station
Tool-less/skill-less flux thickness setting saves product change-over time drastically.

2.Nozzle station (ANC : Auto Nozzle Change)
Auto nozzle changer handles chip size range from □2 to 30mm minimizing product change-over time.
*Example of measurement results with shaft-spindle stopped

3.Wafer feed unit
Wafer feeder with wafer expander & theta alignment mechanism as standard feature.

Promotional Video
Product Specifications
ITEM | DETAILS |
---|---|
Product Name | Package Bonder |
Model | YSB55w |
Applicable substrate | L240 x W200 to L50 x W50mm |
Substrate thickness | 0.2 to 3.0mm |
Transport direction | Left to Right (option : Right to Left) |
Bonding accuracy | ±5µm (3σ) (When using Yamaha's standard components) |
Throughput | 13,000UPH (Including processing time) |
Applicable wafer size | 12 inch wafer |
Applicable die size | □2 to 30mm |
Power supply | 3-Phase AC 200/208/220/240/380/400/416V ±10% 50/60Hz |
Air supply | 0.45MPa or more |
External dimension | L2,090 x D1,866 x H1,550mm (YSB55w main unit & wafer feed unit) |
Weight | Approx. 3,600kg (YSB55w main unit & wafer feed unit) |
*Specifications and appearance are subject to change without prior notice.