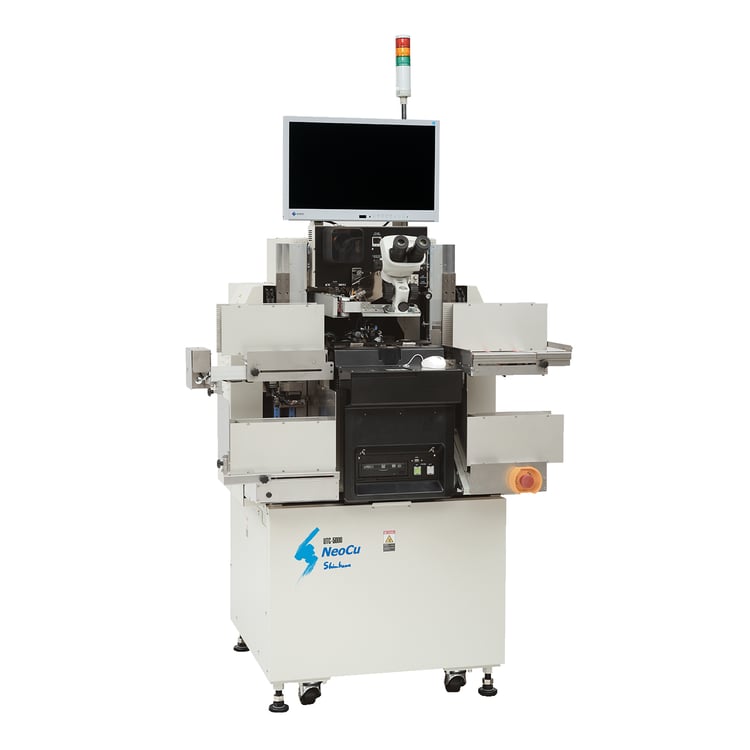
Overview
High-speed Cu wire bonder with advanced features. Upgraded multi-wire model applicable to bonding copper (Cu), palladium-coated copper (PCC) and silver (Ag) wires. Machine performance and functions improved!
- Enhanced parameter setup assistance functions to facilitate product-type startup
- Reliable production by monitoring equipment status
- High quality optics for improved recognition
- Elimination of unnecessary bonding motions to increase UPH
- Improved usability with standardized options and user-friendly functions
- Fail-safe to prevent damage due to mishandling or abnormalities
Features
- Wire bonder with new SimLoop as a standard function. Reduced working time with Automated loop shape optimization and Loop shape editor. Approx. 7% UPH increase by Overdrive mode
- Adaptable to bare Cu wire and Pd coated Cu wire
- Shorter product-type changeover time achieved by digitalizing the flow rate of inert gas
- Neo-Spark function achieving stable initial ball shapes, Neo-Cut function effective for fine-pitch bump formation, and Neo-Step function optimizing bonding processes are all standardized
- Platform featuring high speed bonding of 45ms/2mm with completely updated X, Y and Z motors
- Bonding accuracy of ±2.0μm (3σ) achieved
- Capable of high quality bonding with QFN devices and heavy Cu wire by installing a bonding head with a maximum bond force of 1,000gf and highly rigid transducer
- Equipped with electric flame-off unit applicable to wire sizes φ15-50μm without changing units
Usage examples
Connect with chain bonds: Capillary Wedge Bonding (CWB)
NAND flash memories, widely used as a storage medium such as the familiar USB memory stick, and for large-scale cloud servers, are produced by stacking many dies for increased capacity. Signals from the stacked dies are transmitted through bonded fine metal wires. Conventionally, to bond wires on stacked dies, it is necessary to bond the wire, terminate it, and then bond additional wires on the subsequent steps. This is a time-consuming task and has been one of the productivity bottlenecks in NAND flash memory production.
We have developed a high speed bonding method using CWB and CWB with bump (CWBB) technologies which allows multi-stack wire bonding in a single, continuous cycle without terminating wires. We continue to refine this technology so that a wide range of customers can benefit from its short cycle time.
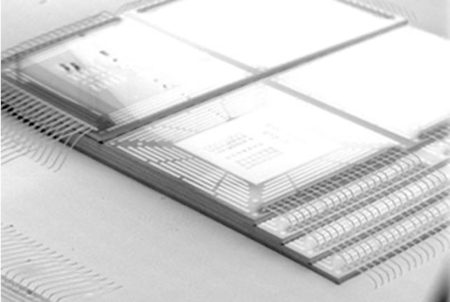
From connecting to making: the wire bonder as electronic device manufacturing equipment
Conventionally, a wire bonder has been widely used as a machine for connecting electrical signals. The connecting demand will never go away, and in fact, it has propelled us to create a wire bonder that can place and shape wires freely. Its capability allows the wire bonder to evolve into an electronic component manufacturing machine by creating coils – important parts of electronic components.
For example, it is possible to create coils with specific impedance or create supplementary coils for circuit adjustment. We are continually working on new challenges based on wire bonding technology.
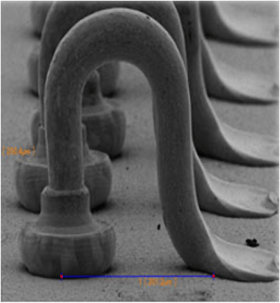
Bond Inspection Measurement (BIM)
BIM is the capability to correct bonding position by feedback of the positional deviation of each bonding position from the pad center using images captured after bonding. It corrects in real time any positional deviation due to disturbances during the bonding operation, and stabilizes the bonding accuracy.
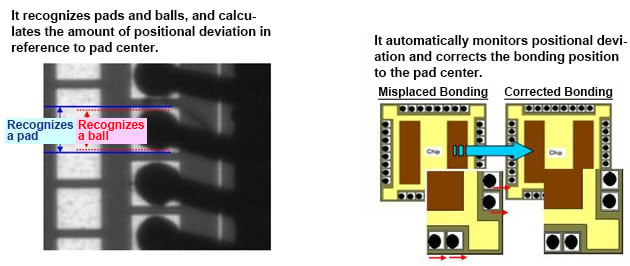
Free Air Ball Measurement (FAM): Automatic free air ball size monitoring capability
FAM is our unique technology which monitors free air ball (FAB) diameter during wire bonding, and detects its abnormality at the same time, to stabilize the diameter. To detect abnormality, the function to monitor capillary tip position – called Reference Positioning System (RPS) – is utilized. FAM is a key technology to support the highly reliable bonding of the UTC-5000 series.
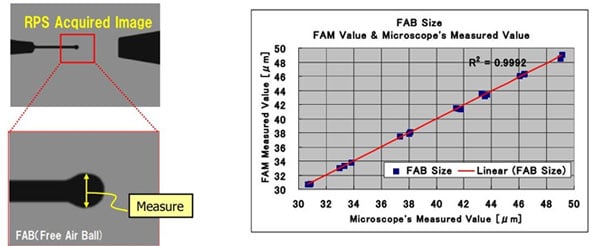
Promotional Video
Product Specifications
ITEM | DETAILS |
---|---|
Product Name | Wire Bonder |
Model | UTC-5000NeoCu Super |
Bonding Accuracy | ±2.0 μm(3σ)Using Shinkawa standard device |
Correction of Bonding Position | System to check and correct capillary offset prior to bonding through Shinkawa RPS (In combination with offset amount correction with temperature detection) |
Bonding Speed | 45 ms/2 mm wire with loop control and force detection mode using Shinkawa standard device |
Bonding Wire Length | 8 mm maximum (Varies depending on device conditions) |
Resolution | XY-table: 0.1 μm Z-axis: 0.1 μm |
Vibration Control | Shinkawa NRS - Non Reaction Servo System |
Bonding Area | X:±28mm, Y:±43.5mm |
Wire Size | Au/Cu/PCC/Ag φ15–50 μm (Bump bonding φ15–30 μm) |
Bonding Force | 3~1,000gf |
No. of Bonding Wires | 30,000 wires maximum |
Loader/Unloader | Fully automatic magazine stacker system (Option: stocker system)) |
Workpiece Size | Width 20– 95 mm (20–93 mm when carrier type) Length 95~300mm Thickness 0.07–2.0 mm (Varies depending on type of device) (Conversion parts are required when thickness changes) |
Production Management | Management of equipment availability through production management monitoring screen |
Options Available | Communication interface SECS-I/SECS-II, HSMS, GEM |
Utilities | Input Power Supply Single Phase 100 VAC (±5% input variation) 50/60Hz (other voltage requires transformer) Power Consumption Approx. 1.3kVA CDA 500kPa(5kgf/cm2)100L/min Vacuum -74kPa or below (-550 mmHg) (gauge |
Physical Dimensions and Mass | 1,244W × 964D × 2,092H mm Approx.520 kg |
*Configuration and specifications of this machine are subject to partial modification without prior notice.
Upgrade Function List
Sales Point | Function |
---|---|
Easy Setup | Loop Height Measurement (Note 1):◯ Tail-Break Strength Measurement:◯ Tail Length Measurement:◯ Bump-cut Auto Setting:◯ New Overhang Mode : ADVANCE:◯ Cycle Time Measurement:◯ |
Higher Reliability | Self Diagnostic Monitor:◯ Process Monitor:◯ Error Image Log:◯ Lissajous Monitor:◯ |
UPH UP | New Tail Cut Mode : SLOW-S:◯ New Tail Cut Mode : ADVANCE:◯ New Circle Scrub Mode:◯ |
Other Improvement | High Resolution Lens Tube (Note 2):◯ Increased Side Illumination Intensity:◯ Heat Haze Prevention (for NeoCu):◯ RPS Lighting Auto Setting:◯ BI Detection Rate Improvement:◯ FAM Focus Adjustment Optimization:◯ 3D Loop Shape Viewer:◯ Improved UI Operability and Operational Flexibility:◯ Fail-safe Functions:◯ |
*Note 1 : Must be equipped with Programmable Focus Lens Tube (Option).
*Note 2 : Both Standard Lens Tube and Programmable Focus Lens Tube (option) can adopt High resolution lens. It is necessary to readjust the illumination setting due to the change in brightness .